How To Say Cpk
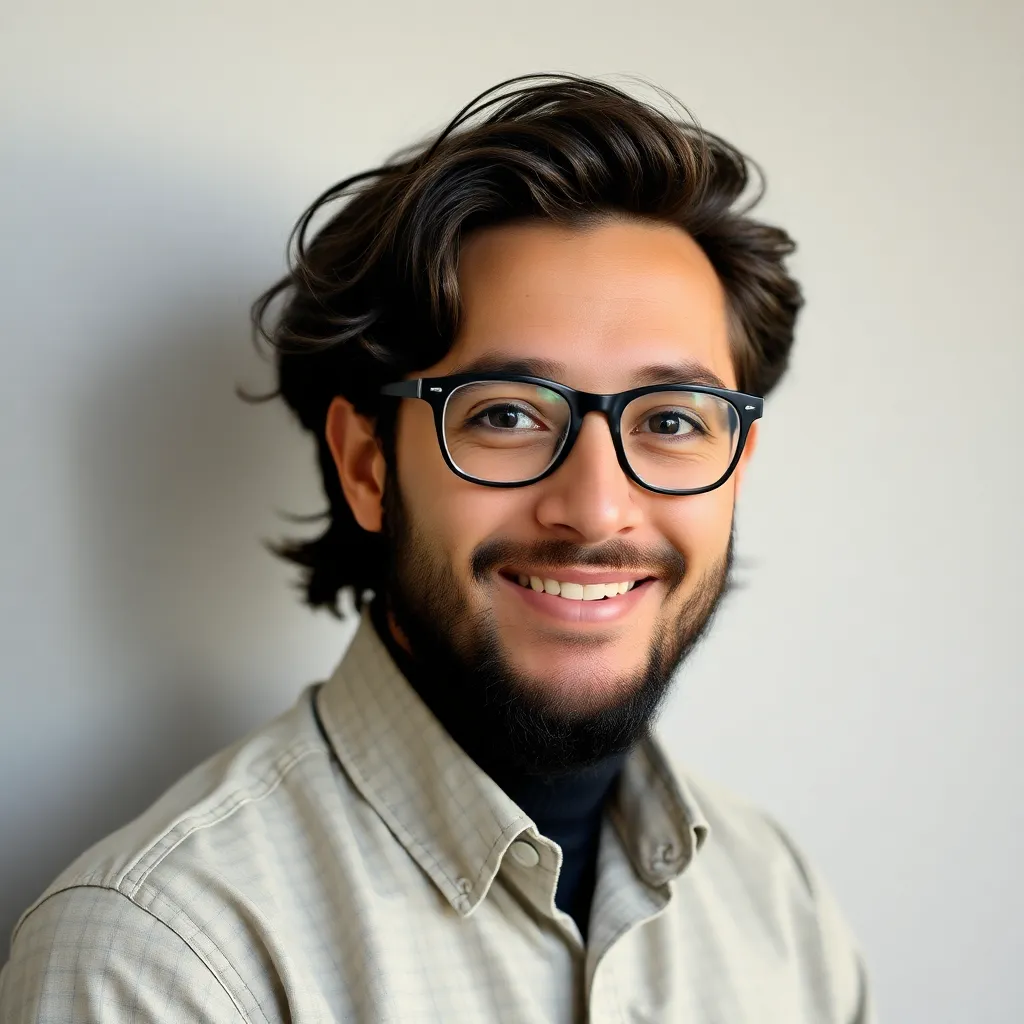
adminse
Apr 02, 2025 · 9 min read
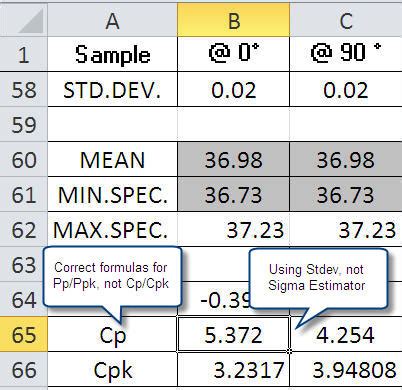
Table of Contents
How to Say CPk: Demystifying Process Capability Index
What makes understanding CPk crucial for quality control?
CPk is the cornerstone of process capability analysis, providing a quantifiable measure of a process's ability to consistently meet specifications.
Editor’s Note: This comprehensive guide to understanding and calculating CPk was published today.
Why CPk Matters
In today's competitive landscape, maintaining high product quality is paramount. Customers demand consistent performance and reliability, and failing to meet these expectations can have severe consequences, ranging from reputational damage to significant financial losses. This is where Process Capability Indices, specifically CPk, become invaluable tools. CPk provides a clear, numerical representation of how well a manufacturing or service process conforms to predetermined specifications. Understanding CPk allows businesses to identify areas for improvement, minimize defects, reduce waste, and ultimately enhance customer satisfaction and profitability. It's not just a metric for manufacturers; it's applicable across various industries, including healthcare, finance, and software development, where consistent process performance is critical. The ability to objectively measure and improve process capability translates directly into a more efficient and reliable operation. Understanding and effectively utilizing CPk is no longer a niche skill; it's a critical competency for anyone involved in process improvement and quality management.
Overview of the Article
This article provides a thorough explanation of CPk, covering its definition, calculation methods, interpretation, and practical applications. Readers will gain a deep understanding of how to calculate CPk, interpret its results, and use this information to improve process performance. We will explore the relationship between CPk and other process capability metrics, such as Pp and Ppk, and discuss the limitations of CPk and when alternative methods may be more suitable. Finally, we will provide practical tips and examples to help readers effectively implement CPk analysis in their own work.
Research and Effort Behind the Insights
The information presented in this article is based on extensive research, drawing from leading statistical quality control textbooks, industry best practices, and real-world case studies. The calculation methods and interpretations are consistent with established statistical principles and are designed to be readily applicable across various industries and contexts.
Key Takeaways
Key Point | Description |
---|---|
CPk Definition | A measure of process capability that considers both process centering and spread relative to tolerances. |
CPk Calculation | Involves calculating the mean, standard deviation, and tolerance limits of the process. |
CPk Interpretation | Higher CPk values indicate better process capability; values below 1.33 generally suggest improvement needed. |
Relationship to Pp and Ppk | CPk incorporates both process centering (Cpk) and process variation (Ppk). |
Applications of CPk | Process improvement, quality control, identifying variation sources, reducing defects. |
Limitations of CPk | Assumes normality, may not be suitable for all processes, sensitivity to outliers. |
Smooth Transition to Core Discussion
Now that we've established the importance of CPk, let's delve into the specifics of its calculation and interpretation. We will begin by defining CPk and then proceed to explain the steps involved in its calculation, using clear examples to illustrate the process.
Exploring the Key Aspects of CPk
-
Defining CPk: CPk (Process Capability Index) is a statistical measure that assesses the capability of a process to produce output within specified tolerance limits. It considers both the process's inherent variability (standard deviation) and its centering (how close the process average is to the target value). Unlike Pp and Ppk, CPk accounts for both aspects, providing a more comprehensive picture of process performance.
-
Calculating CPk: The calculation involves several steps:
- Determine the Upper and Lower Specification Limits (USL and LSL): These are the maximum and minimum acceptable values for the process output, defined by the product design or customer requirements.
- Calculate the Process Mean (x̄): This is the average of the measured process outputs.
- Calculate the Process Standard Deviation (σ): This measures the variability or spread of the process data.
- Calculate CPk: The formula for CPk is:
CPk = MIN[(USL - x̄)/(3σ), (x̄ - LSL)/(3σ)]
. The smaller of the two values represents the CPk. The factor of 3 represents the ±3σ limits, encompassing approximately 99.73% of the data in a normally distributed process.
-
Interpreting CPk: The interpretation of CPk values is crucial. Generally:
- CPk < 1.0: Indicates the process is incapable of meeting specifications; significant improvements are needed.
- 1.0 ≤ CPk < 1.33: Suggests the process is marginally capable; further improvements are recommended.
- 1.33 ≤ CPk < 1.67: Indicates an adequately capable process; monitoring is important.
- CPk ≥ 1.67: Suggests a highly capable process; maintaining current performance is key.
-
CPk vs. Pp and Ppk: It's crucial to understand the distinctions:
- Pp: Process potential, considers only the process spread and doesn't account for process centering.
- Ppk: Process performance, considers both spread and centering but is not standardized.
- CPk: Standardized process capability index, considering both spread and centering, offering a better measure for comparing processes.
-
Improving CPk: Once a low CPk value is identified, several actions can be taken:
- Identify and eliminate sources of variation: Use statistical process control (SPC) tools such as control charts.
- Improve process centering: Adjust process parameters to bring the mean closer to the target value.
- Reduce process variability: Improve equipment maintenance, operator training, and raw material consistency.
Closing Insights
CPk is a powerful tool for evaluating and improving process capability. By understanding its calculation, interpretation, and practical applications, organizations can significantly enhance their quality control efforts. The focus should always be on continuous improvement, using CPk as a benchmark to track progress and identify areas requiring attention. A consistently high CPk value reflects a robust and reliable process, leading to increased customer satisfaction, reduced waste, and improved profitability. While CPk assumes a normal distribution, its application extends widely, proving invaluable in diverse fields. Remember that a high CPk value is not just a number; it's a testament to a well-managed and efficient process.
Exploring the Connection Between Data Analysis and CPk
Data analysis plays a fundamental role in determining CPk. The accuracy of the CPk calculation heavily relies on the quality and integrity of the collected data. Insufficient data, outliers, or non-normal distributions can significantly skew the CPk value and lead to incorrect conclusions. Robust data collection methods, proper data cleaning techniques, and the use of appropriate statistical tests are crucial to ensure the reliability of the CPk analysis. For example, if a significant number of outliers are present, robust statistical methods may be necessary to accurately assess the process capability. This requires careful analysis and potentially the application of different statistical techniques. The role of data analysis extends beyond the initial calculation; it's crucial for identifying the root causes of low CPk values and for monitoring process improvement efforts over time.
Further Analysis of Data Analysis in CPk
The importance of data analysis in CPk is multifaceted:
Aspect of Data Analysis | Significance in CPk | Example |
---|---|---|
Data Collection | Accurate and representative data is essential for reliable CPk calculation. | Using a random sampling method to collect data, ensuring a sufficient sample size. |
Data Cleaning | Removing outliers and dealing with missing data are crucial steps to prevent bias. | Identifying and handling outliers through statistical methods or investigation of causes. |
Descriptive Statistics | Mean, standard deviation, and range provide insights into process performance. | Calculating the mean and standard deviation to determine the process center and spread. |
Normality Testing | Assessing if the data follows a normal distribution is important for CPk validity. | Performing a Shapiro-Wilk or Kolmogorov-Smirnov test to check for normality. |
Hypothesis Testing | Comparing CPk values across different processes or time periods. | Using a t-test or ANOVA to compare CPk values between two or more groups. |
FAQ Section
-
Q: What does a CPk of 1.5 mean? A: A CPk of 1.5 indicates an adequately capable process, suggesting that the process is producing output within specifications with a reasonably low probability of producing defects.
-
Q: What if my data isn't normally distributed? A: If your data isn't normally distributed, using CPk might be misleading. Consider transformations (like logarithmic or square root) or non-parametric methods.
-
Q: How often should CPk be calculated? A: The frequency depends on the process stability and criticality. Regular monitoring (e.g., monthly or quarterly) is usually recommended, especially for critical processes.
-
Q: What are the limitations of CPk? A: CPk relies on the assumption of normality and is sensitive to outliers. It doesn't account for all aspects of quality, such as customer satisfaction or functional performance.
-
Q: Can CPk be used for service processes? A: Yes, CPk can be applied to service processes by defining appropriate specification limits and measuring relevant variables.
-
Q: How can I improve a low CPk value? A: Focus on identifying and eliminating sources of variation, improving process centering, and reducing process variability through targeted process improvements.
Practical Tips
-
Clearly Define Specifications: Ensure USL and LSL are accurately defined and communicated.
-
Collect Sufficient Data: Aim for a sample size large enough to accurately estimate the process mean and standard deviation.
-
Use Appropriate Statistical Software: Statistical software simplifies CPk calculations and interpretation.
-
Visualize Data: Control charts and histograms can provide valuable insights into process behavior.
-
Investigate Root Causes: Don't just calculate CPk; analyze why the process is performing at its current level.
-
Implement Process Improvements: Based on the analysis, implement corrective actions to improve process capability.
-
Monitor Progress: Track CPk over time to monitor the effectiveness of improvements.
-
Document Findings: Maintain detailed records of CPk calculations, interpretations, and implemented improvements.
Final Conclusion
Understanding and applying CPk is a vital skill for anyone involved in process improvement and quality control. It offers a quantitative measure of a process's ability to meet specifications, enabling data-driven decisions to enhance quality and efficiency. By mastering the techniques outlined in this article, readers can significantly improve process performance, enhance product quality, and achieve better business outcomes. The journey towards high CPk is a continuous process of monitoring, analysis, and improvement, ensuring that processes consistently deliver high-quality results and meet customer expectations. Continuous improvement should be the ultimate goal, not simply achieving a specific CPk value.
Latest Posts
Latest Posts
-
How To Say Multigrain
Apr 08, 2025
-
How To Say Amylase
Apr 08, 2025
-
How To Say Conjunctivitis In Portuguese
Apr 08, 2025
-
How To Say Circle In Hebrew
Apr 08, 2025
-
How To Say Clasp
Apr 08, 2025
Related Post
Thank you for visiting our website which covers about How To Say Cpk . We hope the information provided has been useful to you. Feel free to contact us if you have any questions or need further assistance. See you next time and don't miss to bookmark.